How Brushless Motors work
HPI is proud to offer the #1151 Flux Brushless System for all styles of electric RC vehicles! The first Flux system is perfect for 1/10th scale touring cars, buggies and trucks, able to power your car or truck easily up to almost 50mph with the right gearing and battery!
The Flux Brushless System features the Motiv brushless electronic speed controller and the Warp 5700 brushless motor. To make it easy for you to add an incredible speed boost to any electric car, buggy or truck, you can get the Flux Brushless System in a convenient combo pack, part #1151!
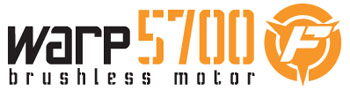
The Warp 5700 is the top choice for nearly all 1/10th scale electric touring car, buggy and trucks. You can go super-fast on the track and get those blazing speed runs with the same motor! With a standard 6-cell NiMH battery pack or 2S LiPo (7.4 volt) pack you can get up to 40mph with just the standard gearing! When geared correctly, the Warp 5700 is equivalent to a high quality 9-turn or 10-turn brushed motor using 6 NiMH cells - a very powerful motor!
The Warp 5700 features:
- Powerful, high-speed brushless motor - equivalent to a '9.5' brushed motor
- Excellent pairing of huge power and extraordinary efficiency
- Same size as standard 540-size motor
- Sleek black-anodized aluminium casing
- Zero maintenance design
- External solder tabs for easy wire replacement
- Oversized precision ball bearings for long life
- High torque, high temperature neodymium rotor
- Slotless stator design delivers smooth, linear torque
- Easy 4-point mounting for convenient installation
- Longer run times than a comparable brushed motor
- Easily rebuildable with bearings and rotor being user-replaceable
- Compatible with any sensorless ESC
#100419 Flux Warp 5700Kv Brushless Motor
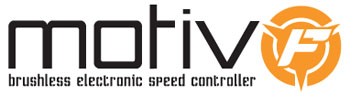
The Motiv brushless electronic speed controller functions as the 'brains' of the Flux power combination. It features easy plug-in connectivity with the Motiv motor series, real Dean's battery connectors for zero-loss power transfer and long switch and receiver leads so you can mount it anywhere in your truck or car. With the capacity to handle different motor sizes, you have the option of different NiMH battery pack sizes and different types of LiPo packs to get the most power out of your Flux Brushless System! It's small in size but huge in power handling capacity! You can even get the upcoming HPI control link to program the Motiv ESC from your computer!
The Flux Motiv speed controller features:
- Reversing brushless/brushed speedo with programmable reverse lock-out for racing
- Small size: 46 x 36 x 23mm (1.8"L x 1.4"W x 0.9"H)
- Extremely light weight: 62.4 g (2.2 oz)
- LiPo programmable low-voltage cutoff**
- High performance cross-cut aluminum heat sink
- Proportional braking for great control off-power
- Huge amount of continuous power handling (70A* Continuous / 380A burst current)
- Smooth startup and run with sensorless motors (Patents Pending)
- Authentic Dean's battery plug for a secure zero-loss connection
- Durable on/off switch
- Simple initial programming
- Ability to easily adjust speedo parameters with HPI link cable (not supplied)
- Up to 8 NiMH cell (9.6) or 2S LiPo compatability with 5700Kv motor, up to 12 NiMH cell (14.4v) or 3S LiPo with 4600Kv motor
- Runs brushless and standard brushed motors (program ESC for type of motor you are using)
*25C temperature, 5mph air flow through heat sink minimum. Burst
current: < 2 seconds duration, 1% Duty cycle.
**ESC must be programmed for Lithium cutoff when using Lithium
batteries.
#100416 Flux Motiv Brushless ESC
The #1151 Flux Brushless System is HPI's answer to hobbyists and racers who want a powerful, versatile and affordable brushless motor system. The Warp motors are extremely powerful, very durable and highly efficient to get you going on the road to victory! HPI Warp motors are sensorless type motors, so there are fewer wires to worry about, and less hassle for you. You can get the Motiv ESC and Warp motor in a set, or buy them separately to outfit all your electric vehicles with brushless power!

Flux Motiv owners can update their speedos with a convenient computer link and free software download! Programmers are constantly making updates to the software loaded onto the Flux Motive speedo, and you can keep up with them by getting the HPI PC USB programming kit. This kit allows you to connect your speedo directly to your Windows PC to save profile settings, customize racing profiles, update the speedo software and more!

The Flux Brushless System can handle a wide range of motors and battery types - please make sure that you use the right combination!
1. When fitted with the Flux Warp 5700 motor or other motors
with 5700Kv of power, you can use up to 8 NiMH cells or a 2S LiPo
battery.
2. When fitted with a motor with 4600Kv of power, you can use up to
12 NiMH cells or a 3S LiPo battery.
The term 'Kv' refers to the number of revolutions per minute (RPM) that the motors will try to deliver per volt (v) applied, and is a standard term for brushless motor power. You might find the letters in various combinations such as 'kv', 'KV' or 'kV' but it's understood in the context of brushless motors that however it's capitalized it all means the same thing!
Available Separately!
The Flux Warp 5700Kv and Motive ESC are also available separately
so you can hop up other cars and trucks!
#100416 Flux Motiv Brushless
ESC
#100419 Flux Warp 5700Kv Brushless
Motor
#1151 Flux Brushless System (with Motiv
ESC and Warp 5700 motor)

First, how brushed motors work
To know why brushless motors are so efficient and powerful, it
helps to know how standard brushed motors work.
In a conventional RC electric motor, such as what you find in the Sprint 2 car or E-Firestorm truck, you'll find two wires (positive and negative) that connect to specific points in the endbell of the motor, two curved permanent magnets inside the case or 'can' of the motor, and a spinning shaft with wires wrapped around it that goes down the centre of the motor can. The shaft and the wires together are known as the 'armature' of the motor, and at one end is where the motor pinion gear is attached - at the other end is a copper section, this is called the 'commutator'.
Touching the commutator to transfer electrical power to the armature are two 'brushes'. As you can see from the diagram above, the wires that come from the speedo bring power to the brushes, which physically contact the commutator, turning the armature into a basic electromagnet when electricity is applied.
How a standard motor spins
When an electromagnet has power applied to it, one end becomes the
north 'pole' and the other becomes the south pole. Because the
north pole of any magnet is automatically repelled from the north
pole of another magnet, the motor armature will want to spin so its
north pole is facing the south pole of the permanent curved magnets
mounted inside the motor can. As the armature spins around to make
the north/south poles meet, the electrical charge applied to the
armature flips, so the poles are again repelled from each other and
they make the armature spin, turning the pinion gear and your car
or truck's transmission. Most electric motors have three poles
instead of two - this prevents the battery from shorting out,
lowering efficiency, and it also prevents the motor from getting
stuck in one position.
The limitations of standard motors
The restrictions of brushed motors are made clear when you need to
get huge amounts of power and speed from them. Because the brushes
must remain in physical contact with the commutator at all times,
there is significant friction from them, especially at high speeds.
Any imperfection in the commutator makes the brushes bounce and
lose contact, making the motor less efficient. This is why racers
true the commutator of their race motors after nearly every run,
and change the motor brushes almost as often. There is also
significant electrical noise generated by the inefficient circuits,
and the commutator and brushes eventually wear out, requiring
replacement of parts of the motor, or the entire thing.
Now, how brushless motors work
The basic explanation of a brushless motor's construction is that
it is similar to a brushed motor, except everything is 'inside out'
and there are no brushes at all. The permanent magnets that would
wrap around the armature in a normal motor are instead placed
around the motor shaft, and this assembly is called the rotor. The
wire coils are around the inside of the motor can, making several
different magnetic poles. In a sensored brushless motor, there are
sensors on the rotor that send signals back to the electonic speed
control.
Why brushless motors are so much more efficient than
brushed motors
Other than the ball bearings the rotor spins on, there is no
physical connection at all, automatically making the brushless
motor more efficient and longer-lasting because there is no
friction of the brushes and commutator. Having a computer (the
speedo) control the rotation of the rotor also vastly increases
efficiency. There's also no sparking from brushes to commutator so
electrical interference is drastically reduced, and finally the
coils are much easier to keep cool, boosting efficiency even
further.
Are there any drawbacks to brushless
motors?
The only possible drawback to a brushless motor system is the
increased starting cost, however anyone familiar with maintaining
high-power, heavily abused brushed motors will know that you'll
quickly see considerable savings because you won't be replacing
motor brushes, brush springs, armatures or whole motors...EVER!
How much cheaper could brushless motors be than standard
motors?
The cost of racing a typical touring car brushed motor could add up
to over 3-5 Euro per run if you replace the brushes every time you
do a 5-minute race. Add in the cost of a variety of springs (four
pairs of springs at 3 Euro per pair), commutator lathe at over 90
Euro, diamond tip for the lathe at over 50 Euro, then the extra
battery pack for the lathe and you've got quite a racing bill on
your hands!
Are brushless motors really 'no
maintenance'?
Yes! They are such a time-saver that racers around the world have
re-discovered the joys of having fun in the pit area. They no
longer have to deal with everything they used to do with their
motors between every race: motor removal, disassembly, comm
trueing, brush swapping, re-assembly, break-in and finally
re-installing...it adds up to quite a lot of time and money spent
every race day!
The only possible need for maintenance are on well-used brushless motors that might need the bearings cleaned or changed. This is only ever rarely needed, however, so it shouldn't even be classified as regular maintenance work.
Why Sensorless?
Apart from basic size and power differences, brushless motors are
available in two main types: sensored and sensorless. Sensored
motors use very small sensors on the rotor, plus an extra set of
thin wires that connect the motor to the speedo, in addition to the
three thick wires that give the motor its power. The extra wires
tell the speedo the position of the motor's armature as it spins,
hundreds of times per second. This provides a huge amount of data
to the speedo, and the speedo's 'brain' takes this data and
combines it with the throttle input from the radio system to make
the motor spin as smoothly and efficiently as possible. All this
makes for a great system for top-level racers, however it makes the
speedos and motors a bit more expensive and slightly harder to
install and use.
A sensorless brushless system, as you might guess, doesn't have these sensors and extra wires, and the motor armature spins without relaying its exact precision back to the speedo every milisecond. This makes the motor and speedo easier to manufacture, simpler to install, easier to adjust and cheaper overall. A sensorless system provides the same amount of power as a sensored type, just with a tiny bit less precision - perfect for sport racers, general hobbyists and pretty much anyone that isn't a hardcore, world-traveling racer.
At HPI, we decided that our customers would almost never need the precision that is available from sensored systems, and we've chosen to use the popular sensorless brushless system for the Flux series.
We hope that this brushless motor primer has explained everything you need to know about why the HPI Flux Brushless System is the best choice for you! As the Flux line expands, you'll be able to get more choice for all your electric speed needs!